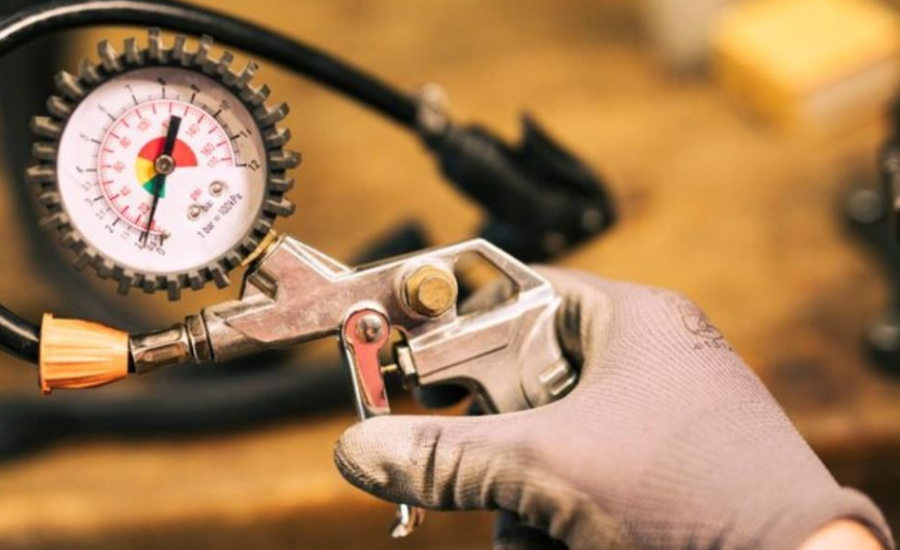
Vacumetros, also known as vacuum gauges, are precision instruments used to measure vacuum pressure in various industries. Unlike standard pressure gauges that monitor atmospheric pressure, vacumetros are specifically designed to measure pressures lower than atmospheric levels. These gauges are critical for ensuring controlled conditions in applications where precise vacuum control is vital. This guide explores the different types of vacumetros, their uses, and why accurate vacuum measurements are crucial in industries ranging from manufacturing to space research.
What Are Vacumetros?
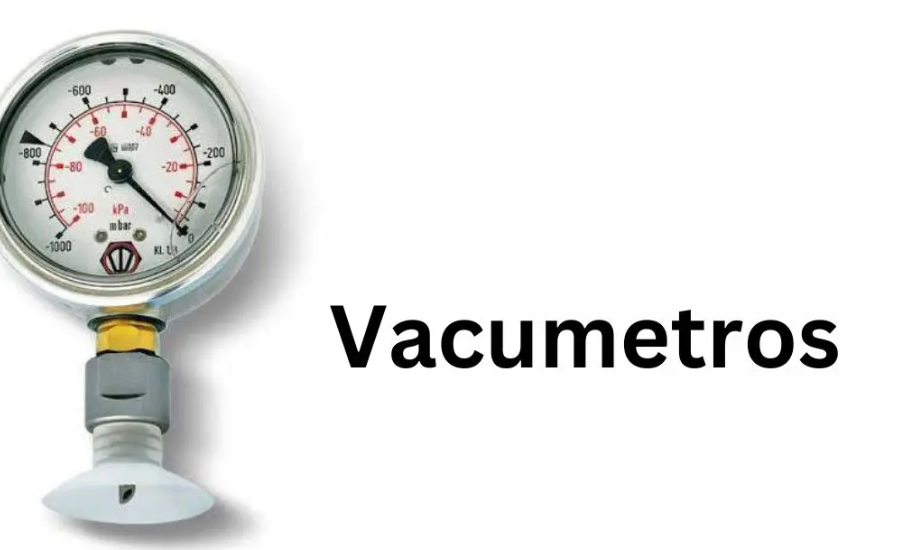
A vacumetro (vacuum gauge) is a device that measures the pressure within a vacuum system. Vacuum pressure is defined as the pressure below atmospheric levels and is crucial for a variety of scientific and industrial processes. By measuring this pressure, vacumetros ensure that systems are operating within their desired vacuum conditions. Whether used in research laboratories, manufacturing plants, or automotive applications, these tools help optimize processes, enhance product quality, and ensure safety.
Types Of Vacumetros: Choosing The Right One
Vacuum gauges come in several varieties, each suited to different applications based on the pressure range and accuracy required. Below are some of the most common types of vacumetros:
1. Mechanical Vacuometers
Mechanical vacuometers include devices such as the Bourdon tube and diaphragm gauges. These gauges operate by measuring the physical deformation of a mechanical element when exposed to vacuum pressure. Known for their durability and simplicity, mechanical vacuometers are often used in environments where high accuracy is not as critical.
- Bourdon Tube: A coiled metal tube that straightens under vacuum pressure, providing a direct reading.
- Diaphragm Gauge: Utilizes a diaphragm that deflects in response to pressure changes, offering a simple yet reliable measurement method.
2. Thermal Conductivity Gauges
Thermal conductivity vacuum gauges, such as the Pirani and thermocouple gauges, measure vacuum pressure based on how gases conduct heat at different pressures. These gauges are particularly useful in low-to-medium vacuum ranges and are favored for their sensitivity to pressure changes.
- Pirani Gauge: Measures heat loss caused by gas molecules in a vacuum and uses that information to determine the pressure.
- Thermocouple Gauge: Uses a thermocouple to detect temperature changes resulting from gas thermal conductivity, providing an accurate measurement of vacuum pressure.
3. Ionization Gauges
Ionization vacuometers, such as hot cathode and cold cathode gauges, are suitable for ultra-high vacuum environments. These gauges ionize gas molecules in a vacuum and measure the resulting ionization rate, making them highly sensitive to very low pressures.
- Hot Cathode Gauge: Uses a heated filament to ionize gas molecules.
- Cold Cathode Gauge: Relies on a magnetic field to ionize gas molecules, allowing it to measure even lower pressures than the hot cathode variety.
4. Capacitance Vacuometers
Capacitance vacumetros are known for their high sensitivity and precision, making them ideal for applications in semiconductor manufacturing and analytical instrumentation. These gauges measure pressure by detecting changes in capacitance between two electrodes within a vacuum chamber. As pressure decreases, the distance between electrodes changes, altering the capacitance, which is then measured to determine vacuum levels.
Applications Of Vacumetros: Essential In Many Industries
Industrial Manufacturing
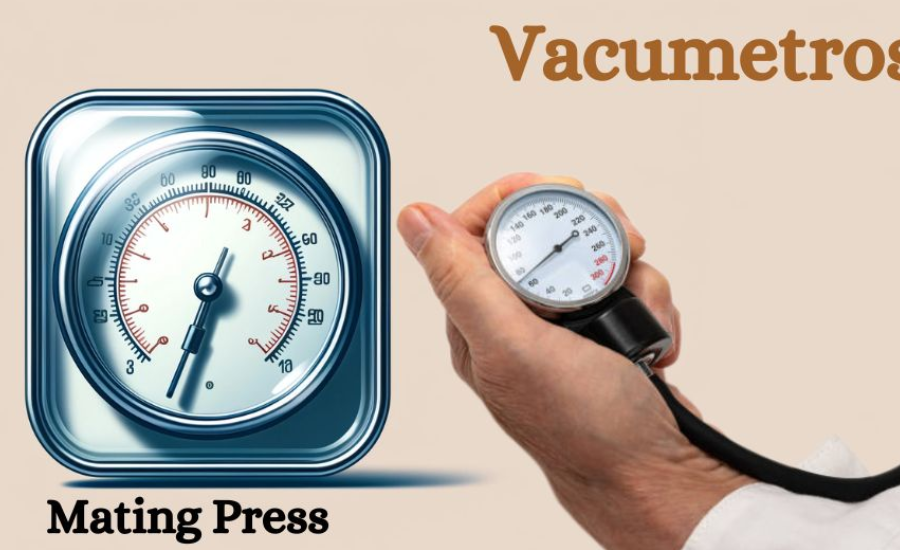
Vacumetros are indispensable in industrial applications that require precise control of vacuum levels. These gauges ensure that processes such as vacuum drying, distillation, and packaging run efficiently and safely. For example, in vacuum drying, vacumetros help monitor the pressure to maintain optimal drying conditions, ensuring that moisture is removed effectively from materials.
Scientific Research and Laboratories
In scientific research, precise vacuum conditions are often required to ensure the accuracy of experiments. Whether used in vacuum chambers, mass spectrometry, or analytical instrumentation, vacumetros help maintain the specific pressure conditions necessary for reliable experimental outcomes.
Automotive Industry
Vacuum gauges play a vital role in the automotive sector, particularly in testing and diagnosing vacuum-powered systems like brake boosters. By monitoring the vacuum levels in these systems, vacumetros ensure that critical safety features are functioning properly and efficiently.
Space Simulation and Aerospace
In the aerospace industry, vacumetros are used in space simulation chambers that replicate the vacuum of outer space. These chambers are used to test spacecraft components and materials under conditions that mimic the extreme environment of space. Accurately maintaining vacuum conditions within these chambers is essential for ensuring the reliability and safety of aerospace technologies.
The Importance Of Accurate Vacuum Pressure Measurements
Accurate vacuum pressure measurements are critical for ensuring the efficiency and safety of various industrial, scientific, and automotive processes. Even small deviations in vacuum pressure can lead to significant issues, such as reduced product quality, process inefficiency, or even system failure. For example, in semiconductor manufacturing, even a slight deviation in pressure can affect the quality of the final product, leading to defects and reduced yield.
Key Considerations When Selecting A Vacumetro
Choosing the right vacumetro for a particular application requires careful consideration of several factors:
- Accuracy and Precision: Look for a gauge that provides the necessary accuracy for your specific vacuum range.
- Pressure Range: Make sure the vacumetro is designed to measure the pressure range required by your application.
- Build Quality: For harsh environments, opt for a rugged and durable device that can withstand extreme conditions.
- Cost vs. Features: Balance the device’s cost with the features and performance necessary for your application.
Maintenance And Calibration Of Vacumetros
To ensure continued accuracy and reliability, regular maintenance and calibration are essential for vacumetros. Here are key practices to follow:
- Regular Calibration: Periodically calibrate the device using certified standards to maintain measurement accuracy.
- Cleaning: Ensure that the sensor components are free from contaminants, which can affect readings.
- Leak Detection: Inspect vacuum systems for leaks, as even small leaks can lead to inaccurate measurements.
- Proper Storage: Store vacumetros in a dry, temperature-controlled environment to prolong their lifespan.
Technological Advancements In Vacumetros
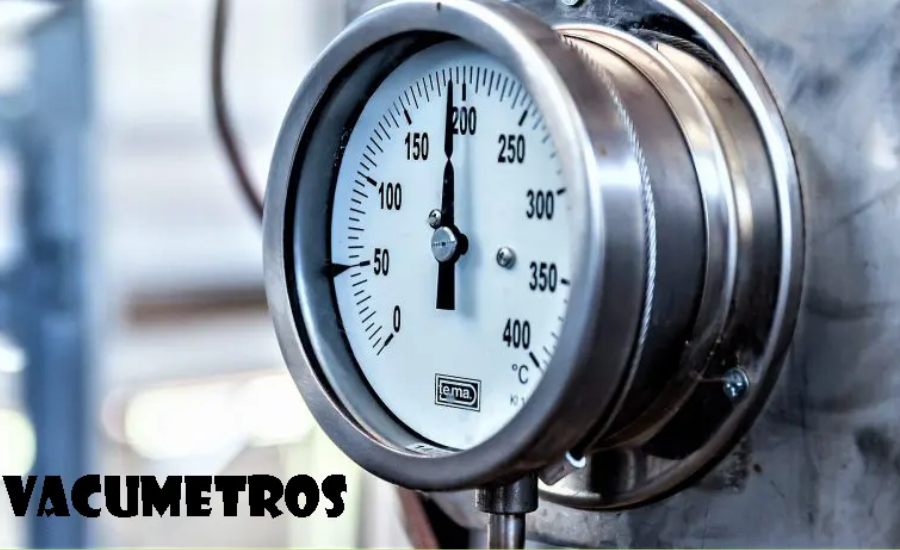
Recent technological innovations have made vacumetros more compact, accurate, and user-friendly. Some key advancements include:
- Miniaturization: Smaller, more portable vacuum gauges now offer the same high level of accuracy, making them ideal for field applications.
- Digital Interfaces: Modern vacumetros often come with digital displays and enhanced connectivity options, making it easier to monitor and record vacuum pressure in real-time.
- Improved Sensor Materials: New materials and technologies have increased the sensitivity and durability of vacuum gauges, allowing them to perform reliably in challenging environments.
The Future Of Vacuum Measurement Technology
As technology continues to evolve, vacumetros are expected to become even more advanced. Future trends include:
- Increased Sensitivity and Speed: With advances in nanotechnology and microelectronics, future vacumetros will be able to detect even smaller pressure changes with greater speed.
- Integration with IoT: The integration of vacumetros with Internet-of-Things (IoT) networks will allow for remote monitoring and predictive maintenance, reducing downtime and increasing system efficiency.
Conclusion
Vacumetros are essential tools for accurately measuring vacuum pressure across a range of industries. From industrial manufacturing to scientific research and aerospace applications, these gauges ensure that vacuum conditions remain optimal for various processes. By understanding the different types of vacumetros, their applications, and the importance of regular maintenance and calibration, industries can ensure that their vacuum systems operate efficiently, safely, and reliably.
FAQs About Vacumetros (Vacuum Gauges)
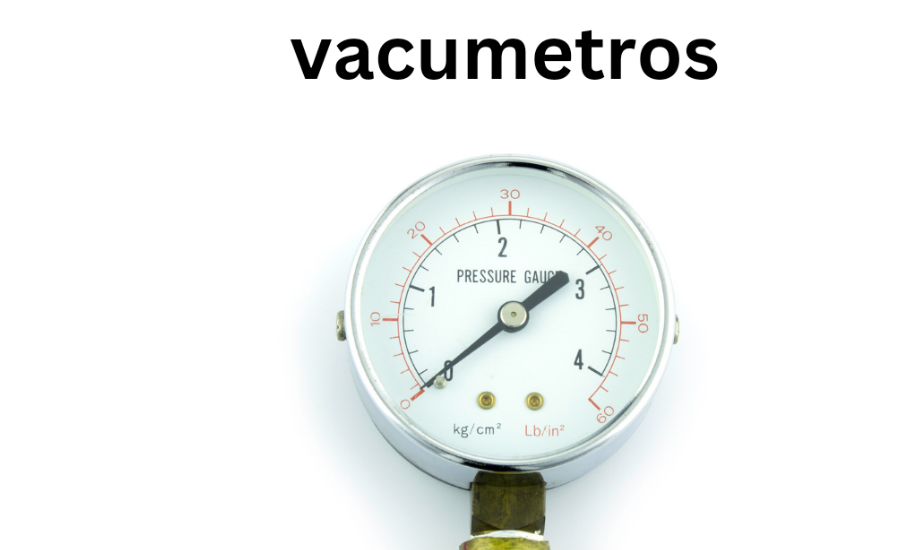
- What is a vacumetro (vacuum gauge)?
- A vacumetro is a device used to measure vacuum pressure, which refers to pressures lower than atmospheric pressure. These gauges are essential for maintaining controlled conditions in various industrial, scientific, and research applications.
- Why are vacumetros important?
- Vacumetros are crucial for ensuring that vacuum systems are operating within desired pressure conditions. Accurate vacuum pressure measurement is vital for optimizing processes, improving product quality, and ensuring safety in industries like manufacturing, research, automotive, and aerospace.
- What types of vacumetros are there?
- The main types of vacumetros include:
- Mechanical Vacuometers: Such as Bourdon tube and diaphragm gauges, often used for lower-accuracy applications.
- Thermal Conductivity Gauges: Like Pirani and thermocouple gauges, used for low-to-medium vacuum ranges.
- Ionization Gauges: Including hot and cold cathode gauges, ideal for ultra-high vacuum applications.
- Capacitance Vacuometers: Known for high sensitivity and precision, typically used in semiconductor manufacturing.
- The main types of vacumetros include:
- How do mechanical vacuometers work?
- Mechanical vacuometers, such as Bourdon tube and diaphragm gauges, work by measuring the physical deformation of mechanical elements (like a metal tube or diaphragm) in response to vacuum pressure.
- What are thermal conductivity gauges?
- Thermal conductivity gauges, such as the Pirani and thermocouple gauges, measure how gases conduct heat at different pressures, allowing them to determine the vacuum pressure by assessing heat loss or temperature changes.
Read Next: Blog Blower